Fallstudie
Betreiber eines Kernkraftwerks
Digitale Transformation mit Fokus auf Akzeptanz und Effizienz
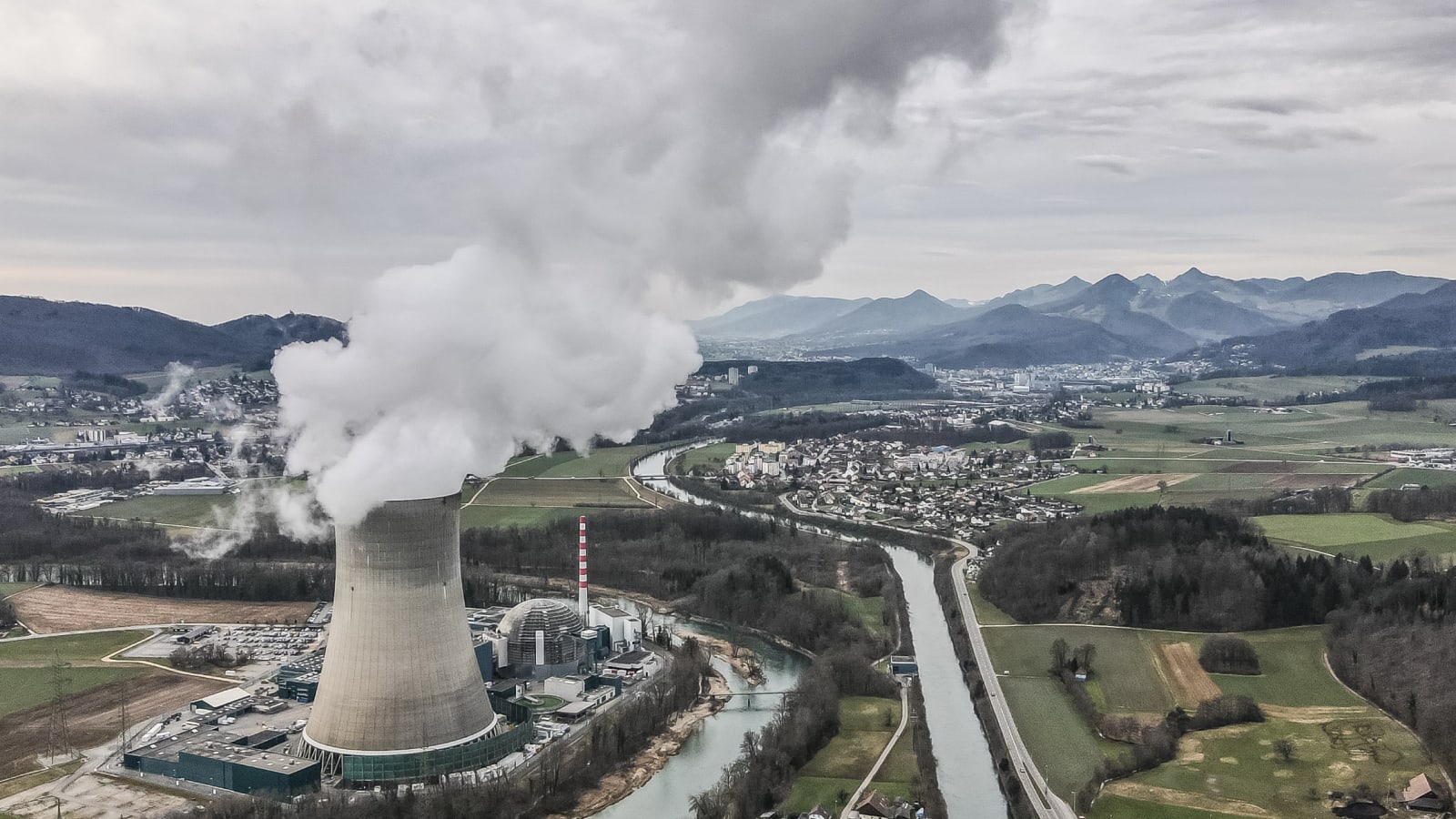
Herausforderung
Der Rückbau von Kernkraftwerken und die sichere Entsorgung nuklearer Abfälle stellen die Branche vor komplexe und regulativ anspruchsvolle Aufgaben. Unser Kunde – ein führendes Unternehmen der Kernenergie – initiierte eine digitale Transformation, um Prozesse zu verschlanken, die Sicherheit zu erhöhen und Innovationspotenziale zu nutzen.
Ziel war es, die Schnittstellen und Abläufe in den Bereichen Endlagerung, behördliche Aufsicht und Zwischenlagerung effizienter zu gestalten – und dabei höchste Anforderungen an IT-Sicherheit und Prozesskonformität einzuhalten.
Ergebnisse & Vorteile durch die Implementierung von Q-Portal
Unser Kunde wollte den Rückbau nicht nur effizient, sondern auch zukunftsfähig gestalten. Mit Q-Portal gelang der Schritt in die digitale Prozesswelt: transparent, sicher und mit hoher Akzeptanz bei allen Beteiligten. Die digitale Plattform wurde zum Schlüssel für ein reibungsloses Zusammenspiel von Zentrale und Standorten – und für echte Effizienz im Rückbau.
1. Optimierung von Schnittstellen & Prozessen
Mit Q-Portal konnte der Kunde Abläufe in Endlagerung, Aufsicht und Zwischenlagerung effizient verzahnen. Redundanzen wurden abgebaut, die Koordination verbessert und Fehlerquellen minimiert – für reibungslose und nachvollziehbare Prozessketten.
2. Ganzheitliches Dokumentenmanagement
Alle relevanten Dokumente werden über den gesamten Rückbauprozess hinweg zentral erfasst und strukturiert verwaltet. So entsteht eine lückenlose, jederzeit nachvollziehbare Dokumentation – als Basis für Qualität, Transparenz und regulatorische Sicherheit.
3. Just-in-Time-Qualitätssicherung
Dank Echtzeitüberwachung können Abweichungen sofort identifiziert und behoben werden. Die durchgängige Qualitätssicherung erhöht nicht nur die Sicherheit, sondern auch die Effizienz in allen Phasen der Stilllegung.
4. Nahtlose Zusammenarbeit zwischen Zentrale und Anlagenstandorten
Von Beginn an arbeiteten Zentrale und Standorte über Q-Portal synchronisiert. Die Plattform fördert den Wissensaustausch, standardisiert Abläufe und schafft eine digitale Grundlage für die standortübergreifende Steuerung des Rückbaus.
5. Nachweise zur Prozesskonformität
Q-Portal erfüllt alle regulatorischen Vorgaben und dokumentiert revisionssicher. Der Betreiber kann jederzeit die Einhaltung von Vorschriften belegen – ein zentraler Faktor für eine sichere und gesetzeskonforme Stilllegung.
Fazit
Die akzeptanzorientierte digitale Transformation mit Q-Portal war ein Wendepunkt für den Rückbau des Kraftwerks. Mit einem einheitlichen, skalierbaren System realisiert der Betreiber nun höhere Sicherheit, Effizienz und Innovationsfähigkeit – kraftwerksübergreifend.
Als Branchenvorreiter setzt der Kunde auf Q-Portal als Standardlösung für den digitalisierten Rückbau – und leistet so einen aktiven Beitrag zu einer sicheren, nachhaltigen Entsorgung radioaktiver Abfälle.